Berlin, January 9th, 2020
How to Tame 10 000 Volt

Case study from company MacroTech.
When Martin Bresch talks about his tasks, there is no stopping him. His enthusiasm for his work shines behind every single word. One of his favourite subjects is the correct approach to learning and working—keep an open mind, observe carefully, don’t tense up too much. This way, with time seemingly complicated tasks can be understood and solved. His career proceeded accordingly, from physicist to company founder of MacroTech as highly specialized enterprise for vacuum evaporation systems. The different fields that Martin Bresch and his staff members at MacroTech work in are very complex. There are only a few experts that are able to understand such a sophisticated refining process that can only be fathomed on a physical and mathematical level. This seems to be par for the course when it comes to developing control solutions and sometimes even complete plants for vacuum coating.
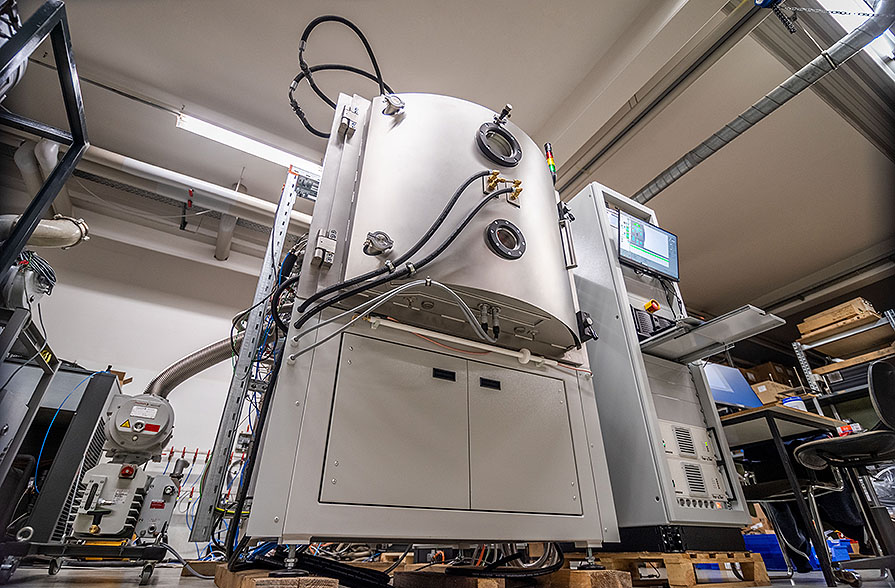
The significance of this coating procedure as a key technology for our modern world cannot be overstated. In fact, basically the whole semiconductor industry operates under vacuum conditions as most processes such as etching, chemical vapour deposition and sputtering all take place in high vacuum. Other fields such as metallization, the optics industry, opthalmology as well as the automotive industry and even the food industry are also dependent on thin coatings for surface refining and hardening.
Macrotech specializes in particular on control solutions for high vacuum coating plants that utilize electron-beam physical vapor deposition, which is done by so-called “electron guns”. For this, the creation of the vacuum with pressure ranges of one millionth of atmospheric pressure and less needs to be controlled by means of pumps, valves and mass flow controllers via pressure-measuring tubes. Likewise, electron-beam physical vapor deposition, ion source, substrate heating as well as the graphical monitoring system need to be accurately controlled. Various materials can be vaporized, including silica, tantalum oxide but also gold, silver, nickel, titan and other metals.

The components such as cameras, sensors, pumps as well as electron-beam physical vapor deposition systems, all come from different manufacturers. The real-time environment is provided by Kithara.
“Without Kithara we would have to program all function ourselves, such as the precise real-time timers. And that would be as inefficient as programming your own operating system or compiler”, Martin Bresch explains. “Kithara Toolkit already includes these functions. Some tools are just required in a ready-to-use state to be able to focus on one’s core skills.”
In order to apply a uniform coating to a product, the electron beam needs to be directed over the material that is to be vaporized by using magnetic coils. However, the beam is not simply moved around back and forth but rather moves in complex, weighted patterns such as ellipses or Lissajous curves.
For fast, reproducible beam deflection, weighted sinus functions, with frequencies between 5 and 50 hertz and suitable phase change in high resolution, are most often passed to deflection coil amplifiers via high-performance EtherCAT modules. This requires an absolutely reliable clock rate with period durations of less than 200 microseconds. To achieve this, MacroTech exclusively uses PC-based controls with the Kithara real-time environment.
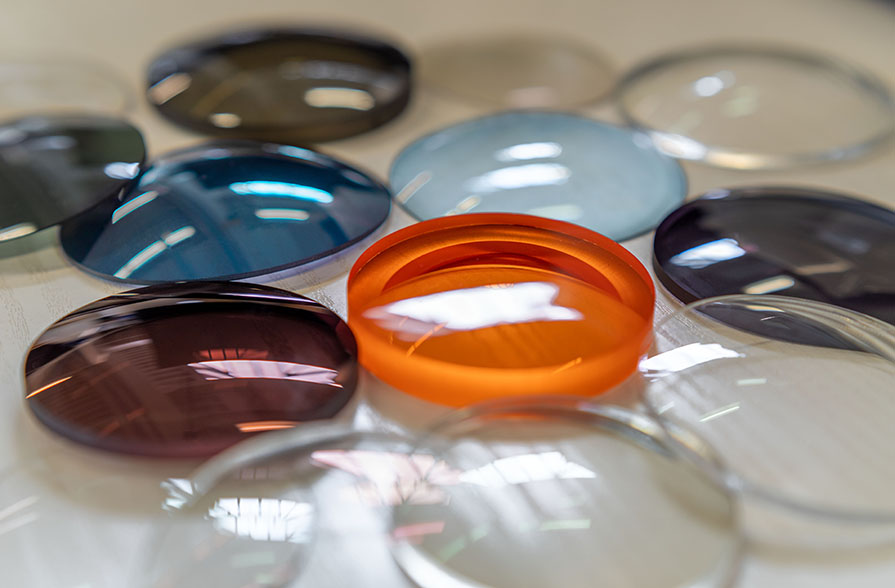
Kithara RealTime Suite allows for easy programming of particularly fast real-time timers with responses in the microsecond range, which is necessary for the output of the deflection patterns onto the coil current amplifiers. The included EtherCAT Master provides direct access to EtherCAT I/O modules without the need for specific interface cards. Further, the Kithara real-time environment is also successfully utilized for conventional control of the vacuum and electron-beam vapor systems including high-frequency timers, access to general I/O, usually with EtherCAT or Profinet, as well as the creation of custom drivers for controlling specific interface cards.
Not an easy task, and not without danger either. If the electron beam, generated from a filament with up to 10000 volt and tamed with accurately controlled magnetic fields, remains in one place too long, even for just a moment, the metal, which is heated up to several hundred degrees, might vaporize uncontrollably. Daniel Köhn, responsible for development, shows us two pocket-watch-sized metal cylinders each with a gaping molten hole in their center.
Also feared are so-called arc discharges, which can occur when the electron beam overshoots its target and the extremely high energy seeks its own path. Similar to lightning storms, this energy suddenly discharges uncontrollably inside the pressure vessel. This makes it obvious very quickly that with these systems, not a single procedure is allowed to remain uncontrolled even for a millisecond.
In order to prevent this, the control solutions developed by Martin Bresch and his team include highly sophisticated algorithms such as for emission current control with intelligent arc management, dynamic adjustment of beam deflection patterns, proactive rate control, intelligent anode current and neutralization control with deposition-rate-based compensation for getter materials as well as locking and enhancing of the shutdown algorithm through linking with the oscillating quartz measurement system for the optical monitoring system.

With such demanding technologies, it is important to maintain a good relationship with customers. Sometimes this would also include MacroTech employees having to travel to Asia to work many hours in order to tame the enormous energies within vacuum. This is sometimes even rewarded with emotional emails. “Tell Martin we love him”, one relieved customer wrote after three days of intensive work by MacroTech. One can hardly wish for a better “Thank you”.
MacroTech Steuerungstechnik GmbH online: www.macrotech.de